Leyland P76 Owners 2006 |
Technical problem |
|
TECH TIPS
ELECTRICAL THEORY, PART 2 BY PROFESSOR PHILTHY, M.A.D.ETC.
Some practical electrical modifications for your P76 borrowed from the Leyland Post, magazine of the Leyland P76 Owners Club of NSW
- In our first big essay about electricity and circuits, and other sparky stuff, we finished with a couple of high-tech drawings of basic electrical circuits, including some with relays.
- In this chapter we will apply some of our new knowledge to our car’s wiring systems, in order to rectify some of the shortcomings which have the potential to cause equipment failures or breakdowns of various kinds.
- In some articles and Tech‑Tips a fair while ago, I described wiring modifications which were pioneered by the honourable Misters Redhead and Nicholson.
- Those modifications were designed to make the wiring systems of P’s more robust and reliable, by eliminating those faults which were ‘built-in’ by the factory as some kind of economy measure.
- It doesn’t take an Einstein to figure out that most mass produced cars are built down to a budget, rather than up to a standard, and it is the compromise between the engineers’ standards and the accountants’ budgeting that causes certain weaknesses or increased mechanical vulnerability to be built into production line cars.
- One of the most expensive factors in the production of a new car is the labour cost, so it should come as no surprise that there are a few critical parts of the various systems on any P where a reasonable amount of time, and a few dollars spent wisely, can go a long way towards curing most of those ‘faults’ in a P which contributed to its ‘lemon’ reputation back in the early days.
- The electrical system has several weak points which are easily fixed if you have a few hours spare to do the job thoroughly, and the hardware required is not expensive.
- Having said that, we have to be practical, and the first item which must be replaced if you are serious about making your P more reliable is the alternator.
- The Bosch alternators fitted to many popular makes of Australian built cars are good reliable units, with a couple of advantages over the Lucas units which were original equipment on the P76.
- The Bosch alternators have fewer moving parts than the Lucas ones, and are usually cheaper to overhaul, and parts are obtainable all around Australia.
- In addition, they are more easily upgraded to a higher output so you can fit brighter headlights, etc, with no worries about running your battery flat by using your high beams for extended periods.
- From memory, I believe that it was the alternators fitted to the early series of six cylinder Commodores which will bolt straight onto a P76 V8 engine, and the only fiddly modification you might need to make is to install a 1/8” spacer washer between the rear of the lower alternator body and the timing cover of your P's engine, in order to keep the pulley of the Bosch unit in line with the P's crankshaft and water pump pulleys, so that the fan belt does not run at an angle to the other pulleys.
- You should fit a fusible link into the main power cable, between the alternator's + output terminal and the battery's + terminal.
- This will ensure that if a short circuit occurs, you won't fry the alternator, or flatten the battery.
- The fusible link should be rated for about 20% more current than the alternator's stated output.
- For example, if the alternator is rated for 50 amps, your fusible links should be rated at 60 amps minimum.
- To get brighter headlights, you will need to shorten the distance the power has to travel from the power source to the actual headlights.
- This means that the power for the headlights needs to bypass the light switch.
- To do this, most P-nutz fit relays somewhere near the fusebox, and run a new power supply cable fitted with an inline fuse or fuses directly from the battery positive terminal to the relays.
- The output terminals on each relay can be connected to the original terminals on the original P76 fusebox, so that each headlight circuit has its own fuse.
- The original wires which come from the dipswitch can be used to operate the relays.
- Some P's are still operating with original style sealed beam headlights.
- If you're planning to do any serious amount of night driving, do yourself a big favour, and fit a full set of the later model high power sealed beams.
- Take the time to remove each headlight's fuse from the fusebox in turn, so you can focus each new beam independently of the others‑this is best done on a deserted stretch of flat roadway where you won't dazzle the oncoming traffic! A good soaking of the adjusting screws with WD will make the adjustments a lot easier.
- A useful modification to help prevent a flat battery due to the headlights being left on, is to wire the headlights and parking lights to operate through an ‘ignition on’ circuit only.
- This means the light switch takes its power from one of the ignition circuits such as the brake lights supply, or the instruments connection on the fusebox.
- Remember that the ignition key controls the power supply to several important circuits. Just think of the equipment on your P which will only work when the ignition is switched on - brake lights, blinkers, the ignition circuit itself, the engine gauges, the heater fan, and the wiper motor, (which should also work when the key is at the ‘AUX’ position).
- The original P76 wiring harness was a pretty well designed item, but after thirty years of wear and tear, there is always the chance that the insulation of one or more wires will have become chafed or cracked, which means you're running the risk of a short circuit, if your whole system is not protected by inline fuses.
- Take the time to check the condition of all wires which pass through the firewall - is the rubber grommet split or torn - does it support and protect the wiring harness?
- Check the condition of the thick brown power supply cable at the starter motor solenoid - is it heat-damaged or hardened?
- In standard harnesses, this cable brings power from the battery up to the fusebox to feed a number of functions.
- Wire and cables which have become stiff and/or brittle should be replaced or repaired.
- At the back of your P, check the condition of the wiring cluster around the lower rear screen.
- Make sure that the boot hinges are not pinching the cluster, or crushing the insulation of any of the exposed wires. Also make sure that the earth connections for each tail light are clean and screwed down tight.
- Next time you're under the front of your P, check the condition of the insulation on the main battery cable to the starter motor.
- I have found that a length of 1/2" diameter garden hose can be slid over the main cable to provide good protection from chafing and stone damage, etc.
- Now, I've previously mentioned the thick brown cable which runs from the starter solenoid contact, across the plenum chamber wall in a small taped harness, and then down to the fusebox.
- There have been several instances where this cable has been disturbed or dislodged, and subsequently come into contact with a part of the exhaust system, or in some cases, one of the right side extractor pipes.
- The usual result of this happening has been a short, intense electrical fire which usually only gets extinguished when the cable bums or melts right through, creating an open circuit.
- If you examine the wiring in the vicinity of the starter solenoid contacts, you will see that that brown cable shares one of the large solenoid terminals with the heavy main battery lead, which supplies power to the starter motor when the solenoid is switched on.
- I don't believe that there is any valid reason to have the power feed for the fusebox set up in this way.
- I believe that the safest thing to do is the modification which we used on all of our P76 Super Sprint and Dirt Circuit 'Weekend Warrior’ racing specials.
- If you want to do this wiring modification, remember to remove either the positive or negative leads from your battery BEFORE you start doing any work!!!
- This modification simply involves removing that brown cable's terminal from the solenoid connection and cutting off the eye terminal, then blanking off the end of the cable with electrical tape so that there is no chance of the cable accidentally touching the exhaust pipe(s), or bodywork of your P.
- Cut to a suitable length a spare piece of similar size cable to serve as the new power supply lead. Fit a new eye terminal to one end of this new lead, and locate that terminal near the battery's + terminal.
- You will need to fit one of the piggy back double spade connectors to the other end of the new power supply lead, because this end will be plugged back into the spade terminal on the fuse box, on the third terminal from the rear.
- You will need to carefully remove the ‘old’ brown cable's terminal from the fusebox, and press it onto the piggy back terminal on the ‘new’ power supply lead, because there is usually a smaller brown cable joined to the big one, just near the fusebox, and this smaller brown cable is the power supply to the inhibitor relay, when the vehicle is wired up with an auto transmission.
- If you want to be doubly safe, then you should fit an inline fuse holder in the new cable, somewhere between the battery's + terminal and the fusebox.
- If you're planning to fit super power driving lights, or some other power hungry accessories later on, it will be worth your while to fabricate two power leads, so that one can supply power to the car's usual functions, and the other can supply power to the accessories or new/extra equipment such as electric fans and driving lights, etc.
- Electric screen washers are a great improvement on the original ones, and the fitting of an electric screen washers system is a relatively simple job.
- The screen washer motor and bottle unit is usually supplied with a metal or plastic mounting bracket which can be screwed or bolted to the inner wall of the plenum chamber, near the heater fan motor.
- The bottle is moulded with two slots in one side, and these slots allow you to simply slide the bottle down onto the bracket, where its own weight will hold it in place.
- The red wire from the washer motor should go to an ignition‑controlled terminal on the fuse‑box, and the black wire should be connected to the green wire with the black trace, which was previously connected to the top of the wiper motor assembly.
- I have found that the original P76 washer nozzles give a better spray pattern than the cheapy ones supplied in the washer kits, but they are more prone to blockages if dirt gets into the washer bottle.
- By wiring up your electric washers as described above, you can use the existing P76 washer switch on the dashboard to operate the screen washers.
- A common fault with automatic P’s is for the starter to become hard or slow to operate.
- This is particularly common with vehicles which are still using their original factory fitted main battery leads, or which have never had the inhibitor wiring and switch renewed, or cleaned and serviced.
- The inhibitor switch is mounted on the left side of the transmission, and most switches get a fair coating of oil and grime as the years pass.
- Oil is a good insulator, and it only needs a small amount of oil and/or muck to accumulate inside the switch to prevent the switch operating as it should. In addition, the associated wiring tends to become stiff and brittle, and most wiring which has spent twenty something years exposed to high levels of heat and humidity tend to suffer!
- Garth published a brief explanation of one cause of starter motor blues in one of the QLD Club's Newsletters a while ago, and he explained the problem with admirable clarity.
- It seems that the power to operate the solenoid to start an auto P has to travel quite some distance around the engine bay, and there is quite a significant voltage drop due to the excessive amount of wiring involved.
- I don't have an exact figure for wiring in this particular circuit, but you can make your own guess when you look at the published wiring diagrams.
- The power travels from the battery, down to the starter motor/solenoid connections, then through the rear plenum harness to the fusebox, then into the main harness into the cabin, and up to the ignition switch.
- From there, it travels via the main harness, back to the engine bay, through the connectors down to the inhibitor switch mounted on the side of the transmission, and then back up to that relay mounted on the lower, inner left guard, IF the inhibitor switch is working properly!
- The relay operates (maybe), and the power from that small brown supply cable, which is usually joined to the big brown one at the fusebox, goes along the white wire with the red trace, back up through the harness, past the fusebox to say ‘Hi!’, and then goes along the rear plenum harness back down to the switch terminal on the upper side of the starter motor's solenoid cap!
- When it finally gets there, with a bit of luck it will be strong enough to make the solenoid do its thing, and get the starter motor going! You can see that in this factory setup, the inhibitor switch is used as the control switch to energise the relay which sends the power to the starter, so if the inhibitor switch has dirty contacts, you'll have an open circuit in that part of the system, and not much action at the starter motor. You can bypass the inhibitor switch and the relay to isolate the problem area if you are having trouble with a ‘lazy’ starter, by a simple test.
- Firstly, separate and disconnect all of the wires at the inhibitor relay.
- Identify the white/red wire which comes from the ignition switch by getting a helper to turn the ignition key to the ‘start’ position.
- Hold a test light probe on the terminal at the end of each white/red wire.
- The wire which lights up the test lamp when the ignition key is held in the ‘start’ position is the one coming from the ignition switch (I hope!).
- The other wire should be the wire which, in theory, takes the power to the starter's solenoid switch terminal (marked ‘sw’ on the solenoid cap) when the key is turned to ‘start’.
- To determine whether or not the starter is serviceable, touch the terminal on the end of the brown cable to the terminal on the end of the white/red wire which goes to the solenoid.
- At the very least, you should hear the solenoid ‘click’ as it tries to operate. If this test does not give a good result, make up a 2 metre long jumper lead of spare cable which is at least as thick as the wiring used on the P76 headlights.
- Fit a female spade terminal to one end of this jumper lead, and fit that end of the jumper lead to the ‘sw’ terminal on the solenoid.
- Bare the wire on the other end of the jumper lead, and touch the bare wire onto the battery + terminal.
- Now, the starter should definitely come to life!
- If it doesn't, you either have a faulty main battery lead, or else the battery itself is dying, or else the starter itself requires some amount of workshop attention.
- Most auto electricians can do a quick bench test of a starter motor which will identify the problem area(s).
- If you are planning a long trip, or you're simply going off the beaten track in the near future, be wise and pay the sparky to overhaul your starter, particularly if your P has an auto transmission!
- Remember that a good test light will let you do checks for accidental earths as well as checking for live wires, but you must be sure that your test light is in proper working order!
- In a previous Tech‑Tip I described how to fix a flickering fuel gauge.
- Some P-nutz are still reporting trouble with fluctuating temperature gauges.
- In most cases, the problem will be caused by a poor earth connection of the earth wires from the instrument cluster. These are usually earthed to the lower facia panel by a machine screw and nut which also holds the lower panel against the steering column support bracket.
- If the earthing screw does become loose, you can have problems with your gauges, dash lights and horn, too!
- When I did some of my round-Australia treks a few years ago, I took advantage of the knowledge and experience gained from my association with the frequently sideways and silly lads of the P76 Sporting Car Club.
- Several of the NSW Owners Club founding members were also members of the P76 S.C.C, and it was during those first few hectic years of weekend circuit racing during the early 80s that we went a long way towards solving nearly every problem that compromised the reliability and limited the performance of our P76s.
- Often, many different approaches to solving each problem were tried, with the results of our experiments being put to the ultimate test on various Sydney and nearby country circuits.
- From these experiences, the best and workable solutions were identified, and those little gems of knowledge were passed on to the general membership of the Owners Clubs, via the various Club Newsletters.
- I was fortunate to be working with the Honourable Misters Redhead and Nicholson when much of this work was done, and the benefit of that association for me was that, by drawing on the knowledge gained in our racing years I was able to build from mainly second hand parts a P76 which took me right across to Perth, and then home to Sydney via the Top End, and it never missed a beat, and never even looked like overheating, even when I went bush-bashing along the fire trails and back tracks in Kakadu National Park.
- That, of course, was the first Mongrel, with a lot of Targa Executive and Super parts fitted into a fairly straight and mostly rust free Deluxe body.
- Even today, most of those modifications are still of value, as our cars are not getting any younger, so any kind of modification which improves any aspect of our P's performance, handling and reliability has got to be good news, and the time and effort involved in working on a P towards those ends is time well spent.
- And that reminds me ‑
- When most P's suffer overheating, it is usually due to insufficient air flow through the radiator.
- It is quite common to find that the front of a P's radiator is literally covered in assorted bugs, which have become glued to the front row of cores. A careful reverse hosing from the engine side of the radiator towards the grille with a decent garden hose nozzle set on a mild jet spray pattern should dislodge most of the bugs.
- Never use a wire or coarse abrasive brush to dislodge your bug collection, as it is too easy to puncture the core tubes.
- A simple and effective radiator stone screen can be constructed using lengths of the same metal used to make household fly screens.
- The materials needed can be purchased from any hardware shop, and will only cost you a few dollars, yet a home-made stone screen, securely and properly mounted a few inches from the front of your radiator, can save you from an expensive radiator repair in the event of oncoming vehicles throwing up stones and gravel at the front of your P.
- A transmission oil cooler works best when it is mounted in a separate air stream to that which cools the radiator. P-nutz can achieve a significant reduction in engine running temperature by relocating their transmission oil cooler away from the front of their radiator, preferably over towards the spacer panel between the right side of the radiator and the mounting plate.
- In some of our early P76 ‘sports’ sedans, we built small metal frames to support the right side of the radiator, and thus replace the spacer panel, and the ‘air space’ made available provided a good location to mount the tranny cooler, which was sometimes used as a cooler for the power steering fluid when the vehicle had a manual transmission.
- This was also a good innovation, because many circuit racing P's boiled their power steering fluid during sprints and lap-dash events. Remember to install an inline fluid filter in the return line between the cooler and the transmission, or between the cooler and the power steering pump.
- Nulon market an excellent additive which provides additional protection for power steering pumps.
|
|
|
|
Last updated March, 2006 |
This web site may contain Copyright material
If you find any problems with the site, please email the
Web Editor 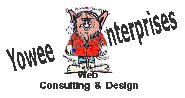 |
|